Understanding why scrapping is a symptom, not a solution
Inventory obsolescence remains a persistent challenge for organisations seeking to optimise working capital and sustain robust profitability. Across many industries, the accumulation of excess stock, and its eventual write-off, is often accepted as an unavoidable cost of doing business. However, this approach overlooks the underlying process inefficiencies that drive such losses and weakens the competitive advantage.
Obsolete inventory typically results from a combination of factors: inaccurate demand forecasting, misaligned supplier strategies, product management oversights, and unforeseen shifts in regulatory, compliance or customer requirements. Over time, these issues compound, leading to increased storage costs, diminished capital efficiency, and repeated financial write-offs. Notably, some organisations even standardise obsolescence by allocating annual budgets for routine scrapping, thereby embedding inefficiency into their operational framework.
The repercussions extend beyond immediate financial losses. Persistent obsolescence undermines process discipline, strains supplier relationships, and limits an organisation’s ability to respond to market changes. While reactive measures may temporarily address symptoms, they fail to resolve root causes or prevent recurrence.
For organisations committed to operational excellence, a proactive, structured approach is essential. The SMART(O) methodology provides a rigorous, systematic framework to diagnose process gaps, recover residual value from excess inventory, and implement controls to prevent recurrence. By shifting from reactive to preventative management, organisations can safeguard margins, enhance supplier collaboration, and sustain inventory performance.
For those seeking to transform inventory management from a source of risk into a strategic advantage, the SMART(O) approach recovers value across your supply chain.
The SMART(O)bsolescence strategy: Turning obsolescence into opportunity
Effective management of excess inventory demands more than reactive measures; it requires a disciplined, proactive framework. The SMART(O)bsolescence strategy: Scrutinise and categorise, Mobilise a sales strategy, Actively promote and discount, Repurpose and rework, Target secondary markets, and Obsolescence management, provides a systematic, stepwise approach designed to maximise value recovery and minimise waste.
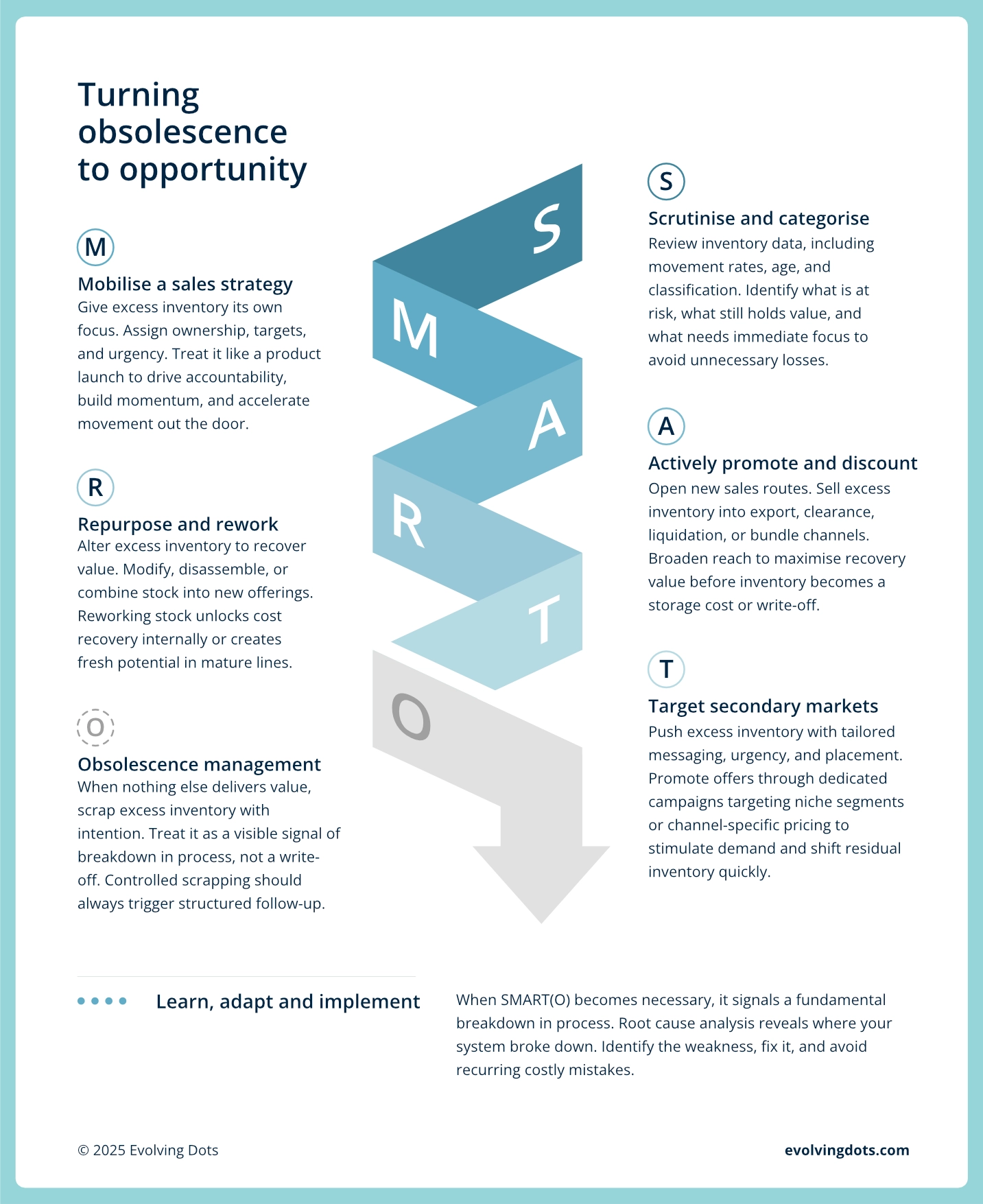
This hypothetical case illustrates how each SMART(O) step is applied to recover value and prevent future excess inventory.
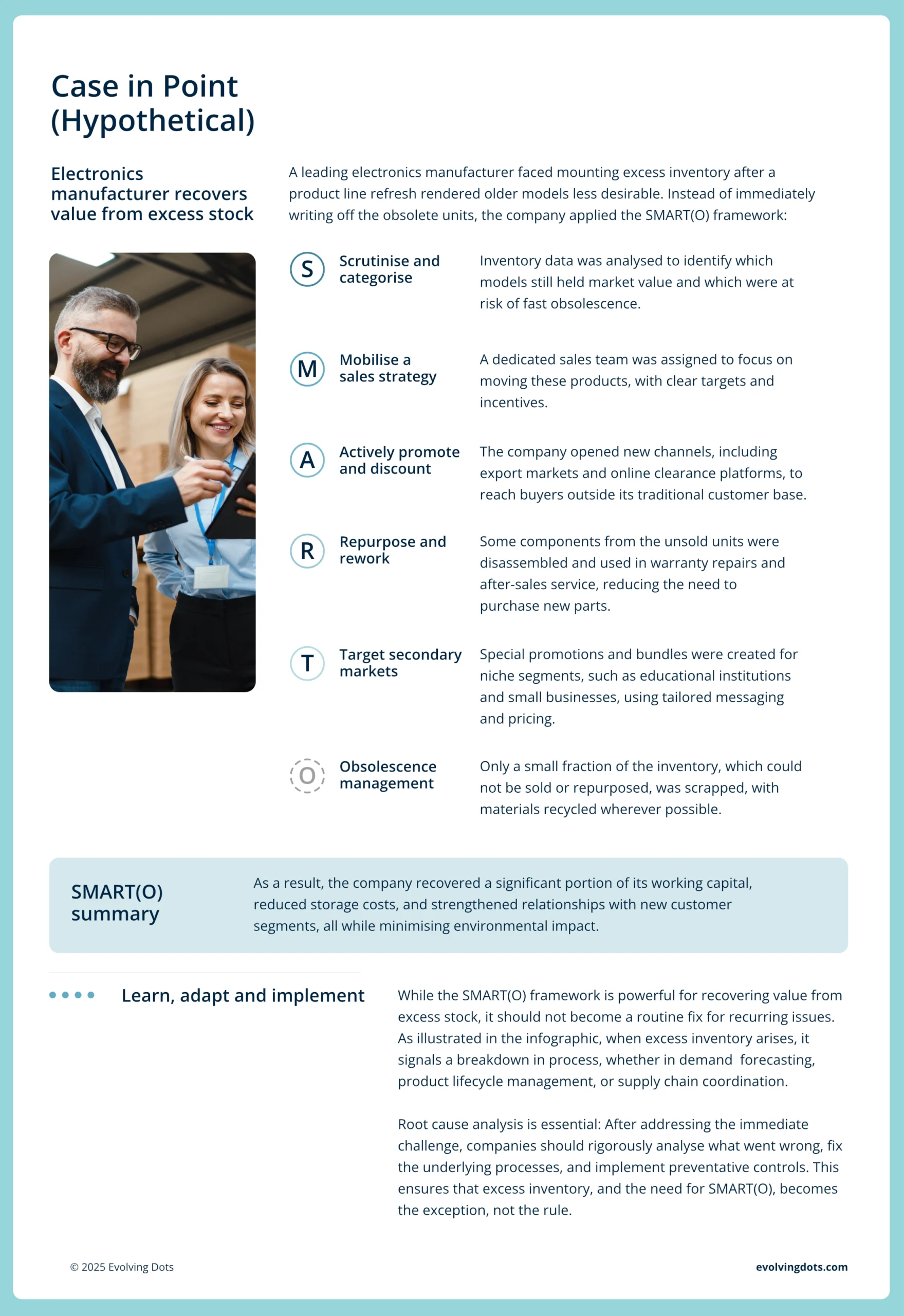
Turn losses into value
SMART(O) embeds visibility, value recovery, and preventative controls throughout the product lifecycle. It replaces margin-draining write-offs with a structured framework that safeguards profitability and strengthens supply chain resilience.
Ready to move from write-offs to value recovery across your supply chain?