Solving issues at the source
We trace recurring problems back to their root and take targeted action to fix, develop or strengthen what is needed. This builds a lean, reliable supply chain that protects service, prevents waste, and increases team productivity while supporting margin growth.
Securing sustainable, high-margin performance
Eliminating systemic failure
Long-term value comes from tracing recurring issues to their root cause and addressing them with precision. We use the DMAIC framework and proven tools like the 5 Whys to uncover failure points hidden in data, process, and governance. This protects margin, safeguards service levels, and frees up working capital.
Sustainable improvements
Structured root cause analysis targets the system, process, and supplier factors behind recurring issues. By replacing reactivity with control, we build a more resilient operation that protects fulfilment, frees up cash, and creates a solid base for profitable growth.

Define
Framing the issue
Pinpoint the problem by mapping where it occurs, how often it repeats, and whose performance it disrupts. Clear definition avoids wasted effort and focuses everyone on what needs to be solved.

Measure
Establishing the facts
Capture the right data, remove assumptions, and align teams around one version of the truth. This gives you a shared, fact-based view to support faster and more accurate decisions.

Analyse
Isolating the root cause
Separate noise from signal to uncover what is really driving the issue. The root cause becomes clear, measurable, and ready to be addressed with confidence and speed.

Improve
Deploying targeted solutions
Turn diagnosis into practical action. Every solution is targeted, measurable, and grounded in your operating reality to fix the issue without creating new ones downstream.

Control
Securing the gains
Lock in improvements with structured reviews, ownership, and early-warning checks. This prevents backsliding, protects performance, and builds long-term confidence in your operations.
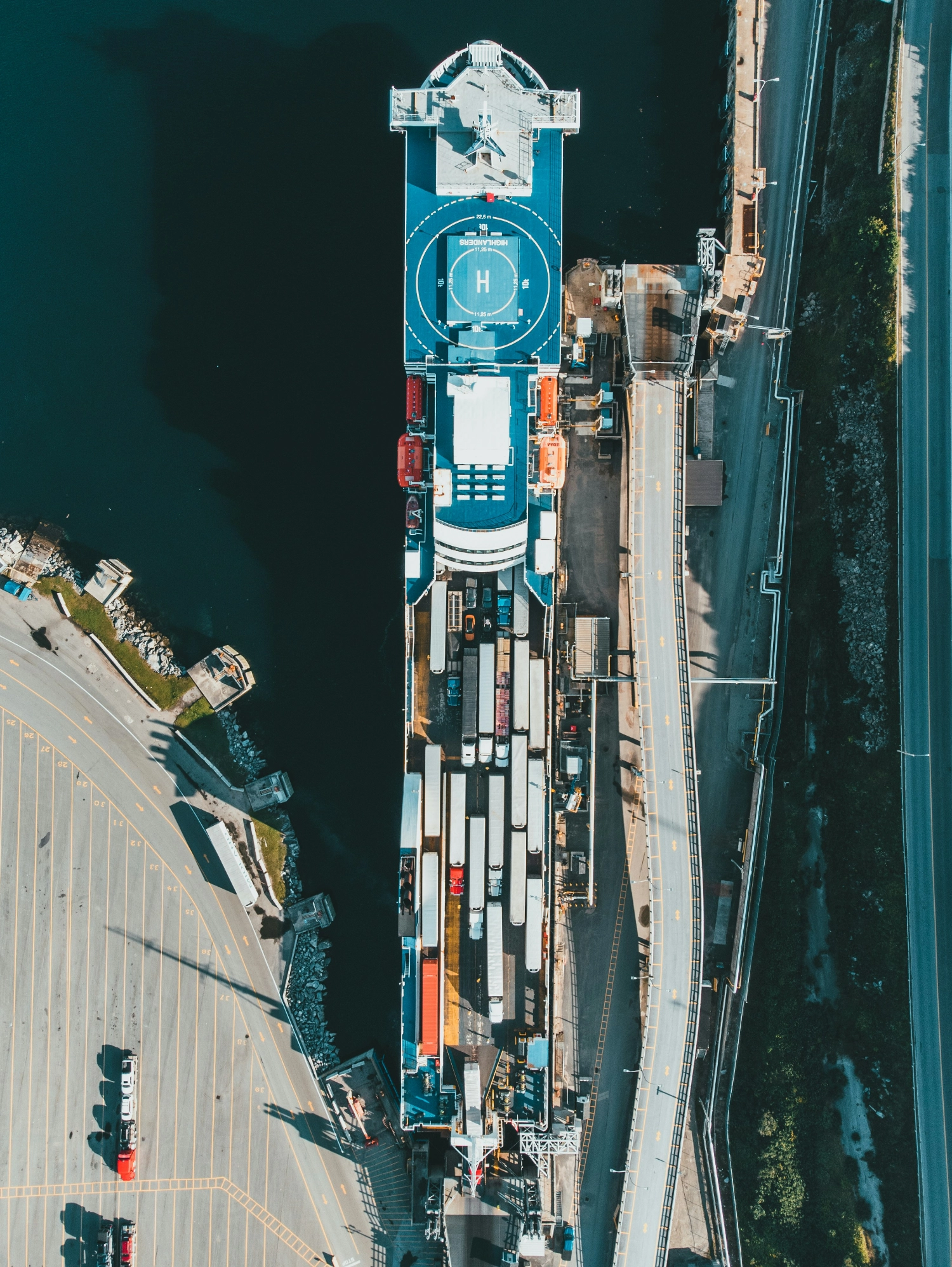
Our Solutions
The risk of ignoring root causes
Operational issues do not fix themselves. Without structured root cause analysis, businesses stay stuck in a reactive cycle of recurring overstock, chronic stockouts, missed OTIF targets and rising operating costs.
✗ Repeating inventory imbalances that immobilise working capital
✗ Supplier delays and rising expediting charges
✗ Planning interruptions slows production, impair service
✗ Growing process costs driven by outdated procedures
✗ Short-term fixes that divert teams from strategic improvement
✗ Revenue leakage through lost sales, write-offs, waste
Fix inefficiencies at the source
We help businesses eliminate the root causes of supply chain inefficiencies, stopping recurring issues and driving long-term efficiency, profitability and control.
Our structured, data-led approach uncovers what is really behind excess stock, fluctuating demand and operational bottlenecks. Using DMAIC, real-time analytics and focused process improvements, we fix the problem at its core and make sure it stays fixed.
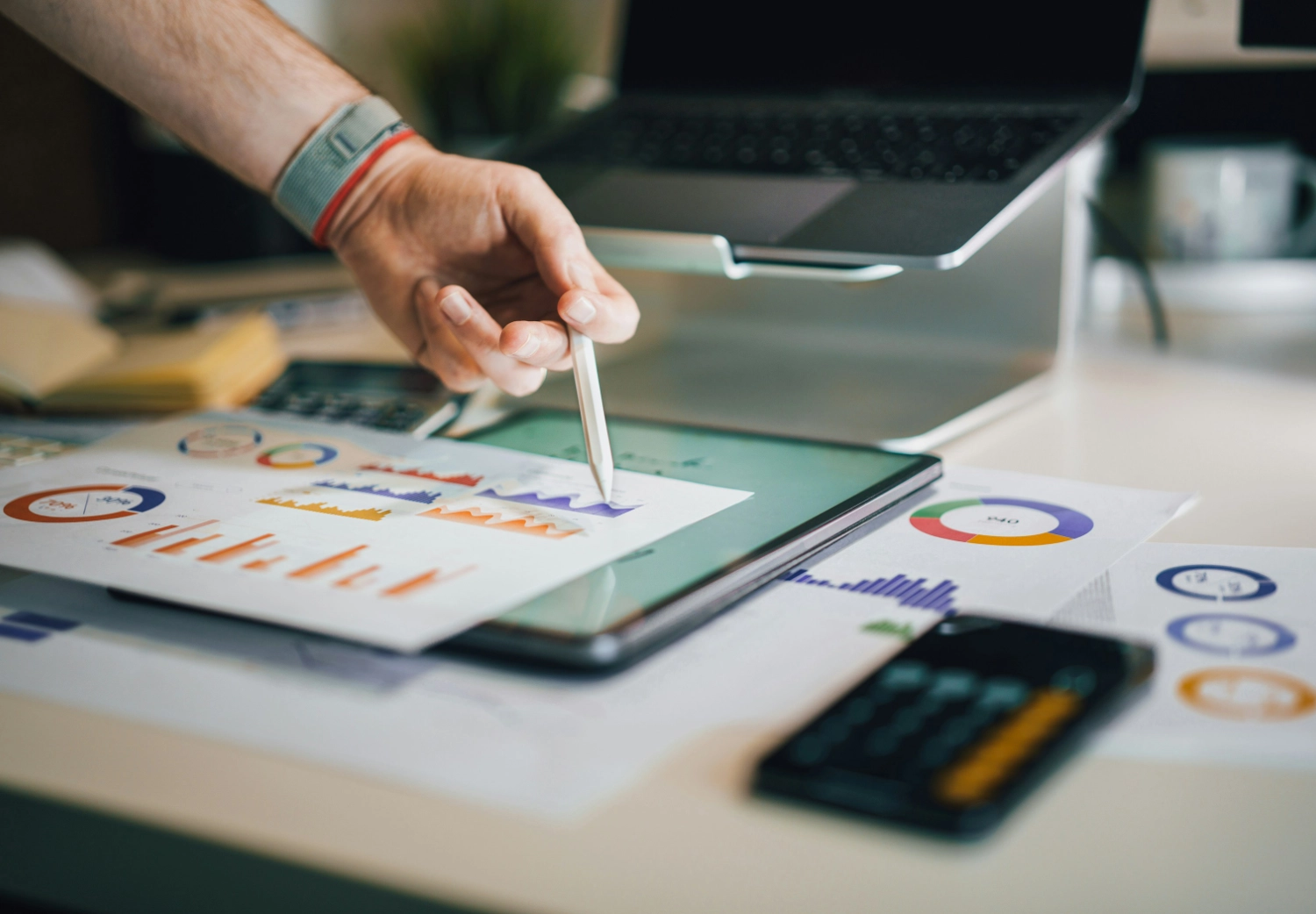
Turn strategies into business cases
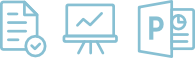
We offer white paper writing and PowerPoint presentations to help businesses share their expertise with clarity and professionalism in their branding. These services are available as add-ons for companies that want to communicate their insights effectively.